A warehouse is one of the critical parts of a supply chain and a mediator between the production line and the subsequent consumption. The efficiency of all warehouse movements and dispositions influences the speed of order processing, and thus, consumer satisfaction and overall business productivity.
The major order fulfillment function at a warehouse is the picking process, which involves retrieving the goods for storage and assembling them for further transportation to the customer.
Picking process advancements are usually introduced with the help of tech tools for inventory management, such as Odoo Inventory Management and Ventor Pro. Let’s learn how they work and help to reorganize warehouse functions.
What is the Odoo Inventory Management System?
The Odoo Inventory Management system is one of the parts of the Odoo ecosystem, which is designed for monitoring, management, and control of warehouse activities and inventory management.
Being a part of Odoo, Inventory Management can be easily integrated with other modules like Sales, Purchasing, Manufacturing, and Accounting to provide a comprehensive approach to inventory operations.
The performance of the Odoo Inventory Management system can also be augmented by utilizing the Ventor Pro app, an Odoo enhancer and barcode application.
Ventor Pro is a mobile-oriented approach designed to bring an extra layer of convenience to warehouse management. It offers an extensive range of features and capabilities to monitor and control warehouse operations, as well as pick goods in your warehouse efficiently.
Given the importance of a picking routine in the overall order processing, let’s learn how this function can be improved with the help of Odoo Inventory Management together with the Ventor Pro application.
Picking Methods by Odoo Inventory Management
Conventional Picking Odoo Methods
- Single order picking (one by one)
Single-order picking is based on collecting one order at a time. It is the most time-consuming and inefficient option, which is only suitable for small businesses that have a low volume of orders and mostly manual data input.
The Odoo barcode app can be used to create an Odoo picking list to guide the person in charge (the picker).
- Batch picking
Batch picking is the first step toward efficiency. Instead of restarting the collection route for every other order, similar products are grouped and picked in batches. It reduces travel time and speeds up order collection.
The Odoo barcode app can help to organize products in batches and thus speed up the picking process.
- Cluster picking
Clusters help to group the goods according to their general criteria—size, destination, category, etc. This method is suitable for large-volume orders and optimizes picking time.
With the help of a picking Odoo list, workers can facilitate and speed up order grouping according to relevant categories and optimize picking time.
- Wave picking
Wave picking is the most advanced form of order picking, which requires better coordination. Orders are divided into waves, each one based on more specific criteria—order priority, product category, or delivery date.
The Ventor app can help to create picking lists and picking waves, and thus manage orders faster.
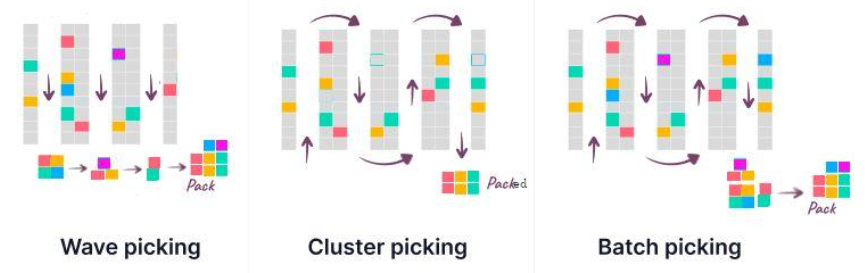
Unconventional Picking Odoo Methods
- Pick-to-light
The light is used as an indicator (a guide for the picker), identifying the goods to pick. Basically, the workers need minimal training, as the technology will identify the zones and items for picking, and the pickers will only need to collect them.
- Voice picking
The voice-picking method is an advanced form of picking. The pickers simply follow the voice commands and pick the right goods.
- Wearable technologies
The pickers can utilize the smart watches or glasses to receive information about the goods to pick.
- Automated guided vehicles
Self-guided vehicles sound rather new for most people, yet this technology is in use in large warehouses. It is often used by pharmaceuticals to increase picking precision and speed.
- Autonomous mobile robots
The robots are more mobile than the vehicles, and they feature the ability to navigate in dynamic and changeable environments.
- Goods-to-person system
This routine involves products being delivered to the picker, which minimizes picker movement within the zones.
The above-mentioned picking formats can be introduced with the Ventor Pro barcode app; yet, their integration will require additional development and adjustments.
How to Optimize Warehouse Picking
- Warehouse layout and picking paths
The warehouse layout is at the core of the routes’ efficiency.
The locations can be categorized into:
- Functional zones – receiving, put-away, storage, picking, packing, and shipping zones.
- Product-based zones – high- and low-turnover, dangerous goods, refrigerated zones, bulk storage, etc.
- Value-added zones – assembly zone, repair, kitting zones.
All the zones should be located according to the frequency of the orders, industry-specific requirements, product characteristics, etc. Analyzing the most frequent routes and making them easily accessible improves order-picking efficiency.
Proper warehouse zoning is responsible for the uninterrupted movement of pickers and faster order collection.
- Technology
Odoo Inventory Management and the Ventor Pro app will provide a solid tech foundation for managing warehouse operations and increasing efficiency of all the interactions within.
- Trained staff
Workers bear plenty of responsibility for proper order picking and processing. Teaching them to use Odoo correctly, create product groups, assign products to specific categories, etc. is critical for a successfully functioning warehouse.
As Odoo software generally features a user-friendly approach, there will be no difficulties in understanding how the system works, and thus, utilizing it correctly.
How to Define the Best Picking Method
The best picking method is crucial for optimizing warehouse performance, and the choice is fully dependent on a few aspects:
- Order volumes
- Warehouse size and zoning
- Product characteristics
- Workforce availability
- Efficiency of tech solutions
- Order processing goals
Usually, warehouse management works out a few picking methods, depending on the above-mentioned criteria. The bigger the warehouse, its order volume, and production diversity, the more picking methods it will feature.
In Conclusion
With the development of technologies, conventional forms of the picking process will be gradually replaced with more advanced forms like voice, light picking, and wearable technologies. Soon, the presence of human pickers will be minimized by utilizing self-guided vehicles and robotic systems.
It is obvious that small warehouses will still make use of traditional Odoo picking methods to simply increase picking efficiency and minimize mistakes.
Yet, large and multi-location warehouses will definitely make use of more sophisticated software, like Ventor Pro, to provide uninterrupted and highly efficient warehouse operations.
Want to discuss your warehouse performance and automation?
Recommended articles:
- Receiving goods in Odoo via a barcode scanner: Receive, putaway, manage lots, serial numbers, packages
- How to build picking routes in your warehouse for walking minimization
- How to create a warehouse map and upload it to Odoo
- Ways to Overcome Logistic Problems with Odoo
- Print product labels from Odoo directly to a printer with 1 click via Odoo Direct Print PRO
----------------------------------------------------------------------
Education: Bachelor's degree.
----------------------------------------------------------------------
Experience:
Marketing manager
VentorTech
----------------------------------------------------------------------
Current position: Marketing manager VentorTech
----------------------------------------------------------------------
B2B Marketing
Google Tag Manager and GA
Motion Graphics Production
0 Comments